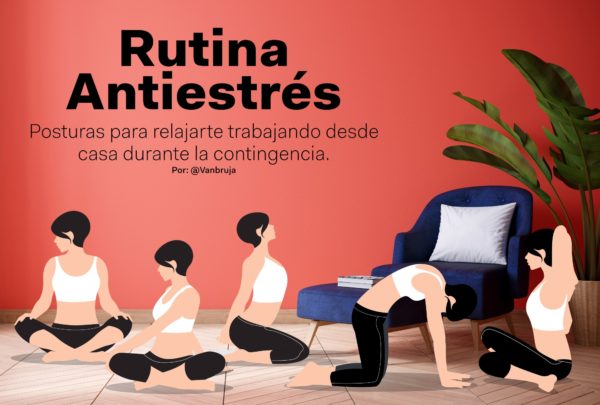
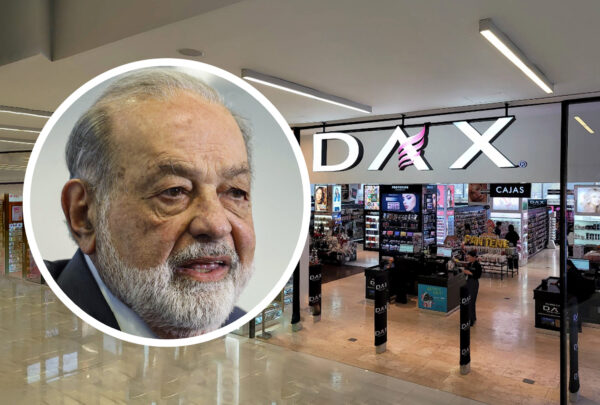
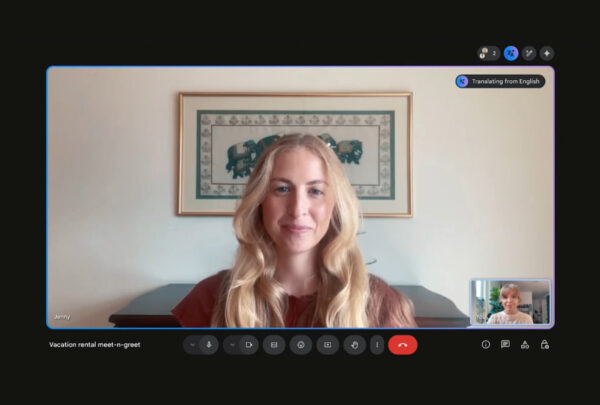
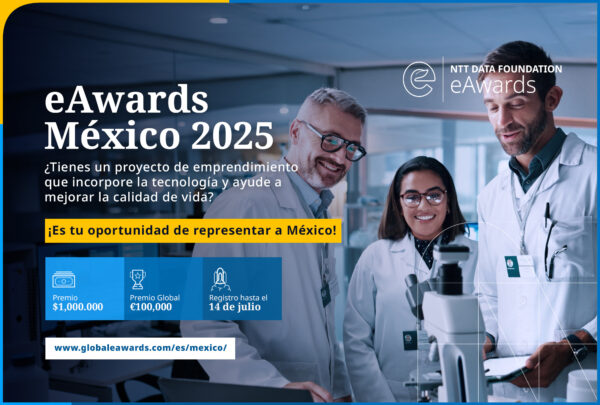
Jaguar enfrenta una caída histórica en sus ventas—hasta 98 % en Europa—tras un controvertido rebranding “woke” y el adelantado fin de sus vehículos de combustión, mientras sus modelos eléctricos aún no llegan a los mercados.
En abril de 2025, Jaguar vendió apenas 49 vehículos en Europa, una disminución del 97.5 % frente a los 1,961 registrados en el mismo mes del año anterior, según datos de la Asociación Europea de Fabricantes de Automóviles.
En noviembre de 2024, Jaguar lanzó una estrategia de imagen que prescindió de sus autos en publicidad, optando por modelos andróginos, colores vibrantes y eslogans como “Copy Nothing”. Aunque buscaba apelar a audiencias jóvenes, generó críticas por desconectarse de su legado automovilístico.
La campaña fue catalogada de “woke” por medios y comentaristas políticos como Nigel Farage y Elon Musk. Expertos apuntan que la estrategia falló al ignorar la conexión emocional de su clientela tradicional.
Jaguar comenzó a retirar sus modelos de gasolina y diésel en previsión de su línea eléctrica. Sin embargo, la primera unidad eléctrica de alta gama no estará disponible hasta fines de 2025 o inicios de 2026. Esta brecha dejó a los concesionarios sin inventario.
Mientras la firma se hunde, rivales como BMW y Audi han visto crecimiento en ventas de EV—32.4 % y 50.4 % respectivamente—y Mercedes mantiene cifras estables, evidenciando que el problema de Jaguar no es del sector, sino propio.
Las ventas globales de la marca han pasado de más de 180,000 unidades en 2018 a menos de 27,000 en 2024. La empresa, bajo Tata Motors, enfrenta una pérdida sustancial en ingresos y reputación.
Para saber más: La audaz campaña de Jaguar que omite sus autos y genera confusión
La firma evalúa a sus agencias de publicidad como Spark44 y Accenture Song. La compañía planea introducir su primer eléctrico (un GT de lujo) en 2026, apuntando a recuperar identidad con su herencia.
El dramático desplome de las ventas de la marca revela los riesgos de una transformación mal gestionada. El intento por modernizar su imagen y alinearse con la movilidad eléctrica sin respaldo de producto ha provocado un vacío que la competencia supo explotar. Jaguar deberá equilibrar innovación y legado para retomar su posición en el mercado del lujo.