LO MÁS VISTO
Guía del emprendedor
Rutina de yoga antiestrés para después de trabajar en casa
Estrés
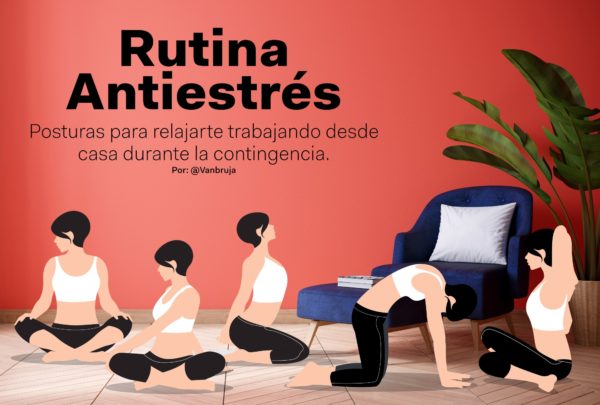
Sin categoría
¿DAX es el nuevo Sanborns de Carlos Slim? Todo lo que se sabe de la cadena tijuanense
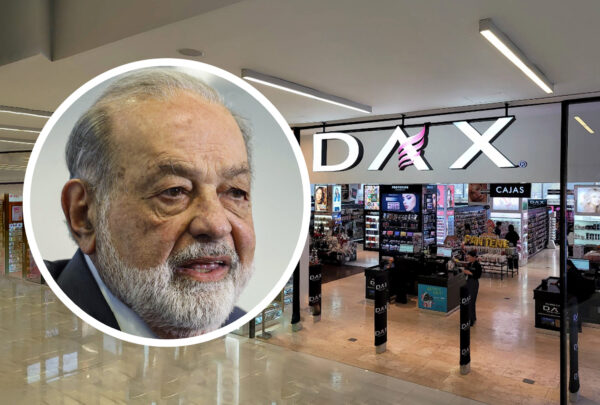
Noticias
¿Videollamadas en inglés? Google Meet lanza traducción en tiempo real con IA usando tu propia voz
Google Meet
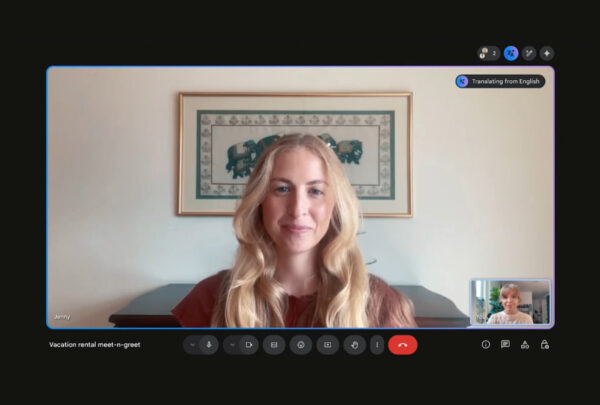
Marketing
Ventas de Jaguar se desploman 98 % tras rebranding ‘woke’
competencia EV
